CORZAN® CPVC
SOLVENT CEMENT WELDING
CORZAN® CPVC
SOLVENT CEMENT WELDING
When installing chlorinated polyvinyl chloride (CPVC) piping systems, you have a few different options to join the piping and fittings. Depending on the pipe size, the pipe and fittings can be threaded or flanged together, each offering a strong, durable union. However, for most applications, Corzan® Industrial Systems recommends solvent cement welding.
Solvent cement is not glue. Instead it is a fast, easy installation process that uses solvents and resin to chemically fuse the pipe and fitting together at a molecular level, essentially creating one continuous piece of plastic. In fact, solvent cement is the only joining method recommended for system features like expansion loops because it allows the pipe to bend and move without breaking or weakening the joint seal.
To ensure the solvent cement is applied properly throughout your process system, follow the process outlined below.
Cutting
Corzan pipe can be easily cut with a ratchet cutter, wheel-type plastic tubing cutter, power saw, or fine-toothed saw. To ensure the pipe is cut square, use a miter box when cutting with a saw. Cutting the pipe as squarely as possible provides the maximum bonding surface area.
Chamfering and Deburring
Burrs and filings can prevent proper contact between the pipe and fitting and may put undue stress on the pipe and fitting assembly. Burrs and filings must be removed from the outside and inside of the pipe. A chamfering tool or file is suitable for this purpose.
A slight bevel should be placed at the end of the pipe to ease entry of the pipe into the socket and minimize the chances of wiping solvent cement from the fitting. For pipe sizes 2 in. and larger a 10 to 15° chamfer of 3/32 in. is recommended.
Fitting Preparation
Loose soil and moisture should be wiped from the fitting socket and pipe end with a clean, dry rag. Moisture can slow the curing, and at this stage of assembly excessive water can reduce the joint strength.
The dry fit of the pipe and fitting should be checked. The pipe should enter the fitting socket easily 1/3 to 2/3 of the depth. If the pipe bottoms in the fitting with little interference, extra solvent cement should be used to prepare the joint.
Primer Application
Use primer conforming to ASTM F656. Primer is needed to prepare the bonding area for the addition of the cement and subsequent assembly.
It is important that a proper applicator be used. A dauber, swab or paintbrush approximately half the size of the pipe diameter is appropriate. A rag should not be used.
Primer is applied to both the outside of the pipe end and inside of the fitting socket, redipping the applicator as necessary to ensure that the entire surface of both is tacky.
Solvent Cement Application
For most applications, use only solvent cement conforming to ASTM F493. Contact Corzan Industrial Systems or the solvent cement manufacturer for recommendations for harsh chemical applications.
Solvent cement must be applied when the pipe surface is tacky, not wet, from primer. Joining surfaces must be penetrated and softened.
Cement should be applied with a natural bristle brush or swab half the size of the pipe diameter. A dauber may be used to apply cement on pipe sizes below 2 in. A heavy, even coat of cement should be applied to the outside of the pipe end, and a medium coat should be applied to the inside of the fitting socket. Pipe sizes greater than 2 inches should receive a second coat of cement on the pipe end.
Assembly
After cement application, the pipe should immediately be inserted into the fitting socket and rotated 1/8 to 1/2 turn until the fitting-stop is reached. The fitting should be properly aligned for installation at this time and the pipe must meet the bottom of the fitting socket.
Then, the assembly should be held in place for 10 to 30 seconds to ensure initial bonding and to avoid push-out. A bead of cement should be evident around the pipe and fitting juncture. If this bead is not continuous around the socket shoulder, it may indicate that insufficient cement was applied. In this case, the fitting should be discarded and the joint reassembled. Cement in excess of the bead may be wiped off with a rag.
Joining of Large Diameter Pipe
For 6 in. or larger diameter pipe, a pipe puller (come-a-long) is recommended to assemble the joint and hold it in place for the initial set time without applying excess force that may damage the pipe or fitting. This equipment should be set up prior to the start of priming so the assembly can happen quickly while primer and cement are still fluid.
Set and Cure Times
Solvent cement set and cure times are a function of pipe size, temperature, relative humidity, and tightness of fit. Drying time is faster for drier environments, smaller pipe sizes, high temperatures, and tighter fits.
The assembly must be allowed to set, without any stress on the joint, per the time shown in the following tables. Following the initial set period, the assembly can be handled carefully avoiding significant stresses to the joint.
Extra care should be exercised when systems are assembled in extreme temperature conditions. Extra set and cure times should be allowed when the temperature is below 40°F (4°C). When the temperature is above 100°F (38°C), the assembler should ensure that both surfaces to be joined are still wet with cement before joining them.
Recommended Set Times
After a joint is assembled using solvent cement, it should not be disturbed for a period of time to allow for proper “setting” of the newly prepared joint. Recommended set times are as follows:
Recommended Cure Times
After a joint is assembled using solvent cement, the cement must be allowed to properly “cure” before the piping system is pressurized. Recommended minimum cure times are shown below. These recommendations should only serve as a guide, since atmospheric conditions during installation will affect the curing process.
High humidity and/or colder weather will require longer cure times: typically add 50% to the recommended cure time if surroundings are humid or damp.
Dos and Don’ts
While not a complete list, the following is intended to highlight many of the “Dos” and “Don’ts” when solvent cementing Corzan® CPVC pipe and fittings.
Dos
- Install product according to the manufacturer’s installation instructions and this manual. Follow recommended safe work practices. Follow proper handling procedures.
- Use tools designed for use with plastic pipe and fittings. Use proper solvent cement and follow application instructions.
- Cut pipe ends square.
- Deburr and bevel pipe before solvent cementing.
- Rotate the pipe 1/8 to 1/2 turn when bottoming pipe in fitting socket.
- Avoid puddling of solvent cement in fittings and pipe.
- Follow manufacturer’s recommended cure times prior to pressure testing.
- Visually inspect all joints for proper cementing at the end of the shift or day. A visual inspection of the complete system and all joints is also recommended during pressure testing.
Don’ts
- Do not use solvent cement that exceeds its shelf life or has become discolored or gelled.
- Do not use solvent cement near sources of heat, open flame, or when smoking.
- Do not pressure test until recommended cure times are met.
- Do not use dull or broken cutting tool blades.
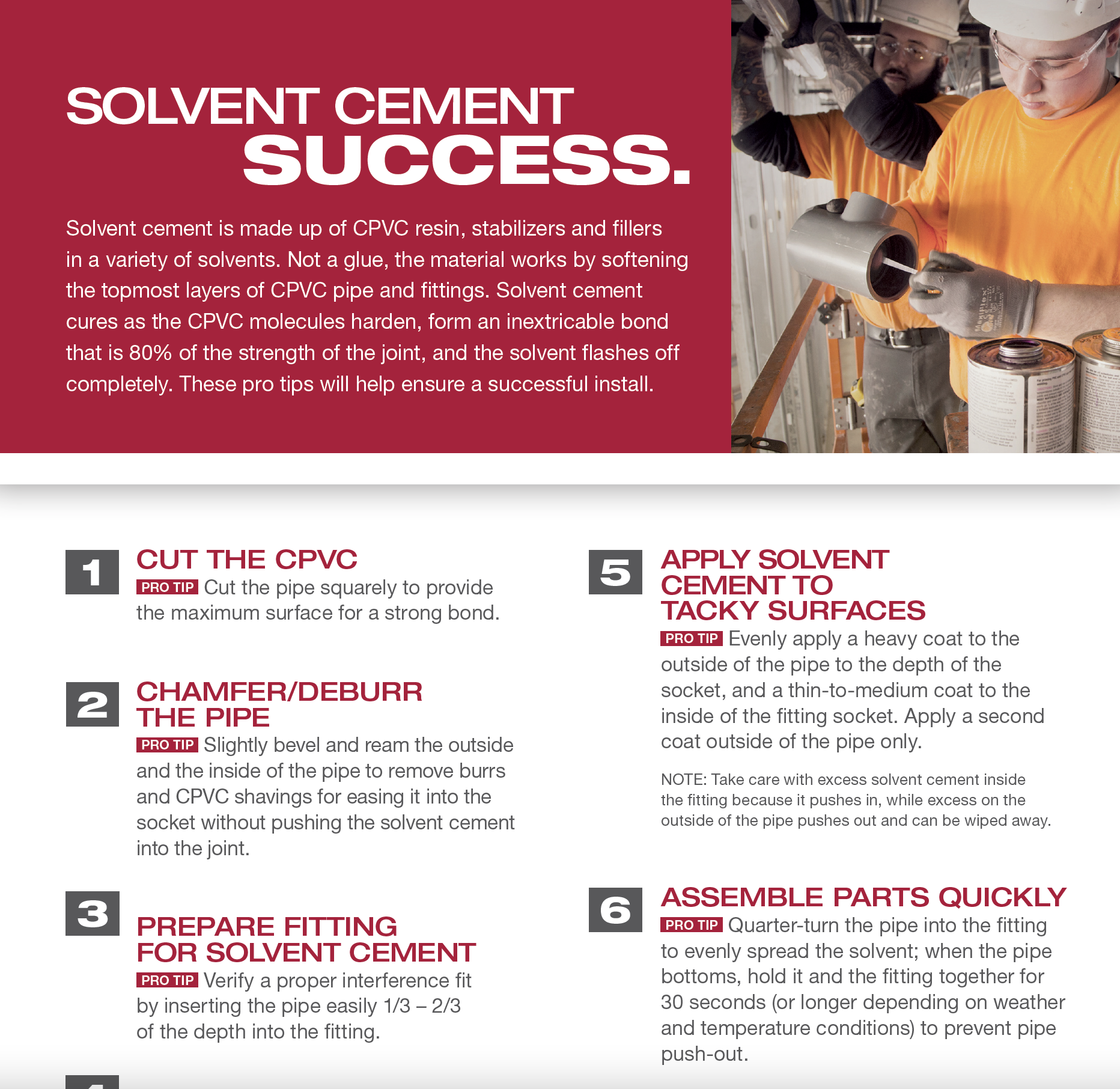
Solvent Cement Success
Solvent cement is made up of CPVC resin, stabilizers and fillers in a variety of solvents. Not a glue, the material works by softening the topmost layers of CPVC pipe and fittings.