Design Requirements for Power Generation Plant Cooling Systems
Power generation plants move large quantities of water, caustics and corrosive chemicals during the power production process. Designing piping systems for these facilities can be a challenge based on the very nature of the chemicals used and the high levels of heat and pressure.
Carefully assessing material choices and selecting the right piping system can directly impact operational efficiency while minimizing downtime and improving bottom-line performance. CPVC is often a viable alternative to metal piping for new and existing power generation plants, delivering advantages such as low installation costs and a lifetime of corrosion-free service.
The Ongoing Corrosion Battle
Thermoelectric power plants boil water that creates steam to turn the turbines used to manufacture electricity. Water cooling systems then cool the steam from the turbine, transferring the steam’s heat energy to the cooling system water, which is then carried away.
Large power plants often use once-through cooling systems that take water from a nearby source such as a lake or river, circulate it through the system once and then return it to the original body of water at a slightly elevated temperature. Smaller plants usually rely on wet-recirculating or closed loop systems that recycle the same water, cooling the liquid in water towers or chillers before reintroducing it into the system.
Piping materials installed in power plants must be compatible with untreated water and/or the chemicals used to treat raw water to prevent corrosion, which can negatively impact efficiency and increase costs. Corrosion has the potential to cause any number of problems, including decreased pressure rating as the pipe’s walls thin. Corrosion can also contaminate the fluid if corroded pieces break off into the flow.
Various systems within a power generation plant depend on cooled water to operate efficiently. A cooling system repair resulting from corrosion may require closing an entire area within a plant, impacting productivity and costs.
Selecting Chemically Compatible Materials
Raw water often falls outside a neutral pH, making it incompatible with metal. Power plants that rely on raw water for cooling processes may be unable to use metal piping since metal will experience accelerated corrosion in the presence of raw water and higher temperatures
CPVC piping systems, in contrast, are made with durable chlorinated polyvinyl chloride and are strong enough to withstand aggressive chemicals – such as hydrochloric acid and sulfuric acid – along with the higher temperatures and pressure common to power plant applications.
The charts that follow demonstrate Corzan® CPVC’s chemical resistance to hydrochloric acid and sulfuric acid.
Corzan CPVC offers excellent resistance to a wide range of corrosive chemicals. The Corzan CPVC Chemical Resistance Chart shows how the product performed when tested with over 400 different chemicals. Keep in mind that any time proprietary mixes are used with Corzan CPVC, the components within the mix must be compatible with CPVC.
Specific use conditions will impact the chemical resistance of thermoplastic piping systems, including CPVC. Variables such as chemical concentration, temperature, pressure, external stress and final product quality can affect a piping system’s resistance to specific chemicals. In-service testing, therefore, is always the best way to determine piping material suitability for a power plant application.
Providing Proper Support for Piping Systems
Piping system hangers and supports must be correctly spaced to help maximize performance. Allowing too much space between supports adds unnecessary stress to the system, causing deflection and sagging. And, too little space will result in unnecessary installation costs.
CPVC piping offers an advantage over other thermoplastics in that CPVC will maintain its structural integrity at elevated temperatures, which means fewer supports are needed. Several factors will impact the distance needed between hangers and supports:
- Pipe diameter. Larger diameter piping will require fewer supports as it is inherently less prone to deflection.
- Increasing temperature. Higher temperatures will cause the material stiffness or flexural modulus of thermoplastics to decrease, thereby requiring more frequent supports.
- Weight of transported fluids. Denser processing chemicals and other fluids will increase demands on the piping system, creating the need for more supports.
- Location of concentrated loads. Additional supports may be required to help support the weight of heavy instruments or system valves.
- Possible fluid accumulation. Processes prone to weight buildup from solids or liquids should increase the number of supports to prevent the piping system from sagging.
Lubrizol developed the following Maximum Support Spacing table for Corzan CPVC Schedule 80 piping, taking into account the pipe size, pipe schedule and processing temperature. The table includes pipe sizes up to 16 inches – although Corzan CPVC is available in sizes up to 24 inches.
Maximum Support Spacing for Schedule 80 CPVC Piping (in feet)
Designers will need to multiply the number appearing in the Maximum Support Spacing table by the number from the following table for piping systems that convey liquids with higher specific gravities.
It is important to secure the pipe with smooth straps or hangers that allow for movement during expansion and contraction. Hanger edges should be smooth or rounded to prevent pipe from becoming scratched or abraded.
Minimizing Surge Pressure
Surge pressure in pipes, or fluid hammer, occurs any time the linear flow rate of fluid in a piping system changes quickly – when pumps start or stop, valves open or close with quick acting actuation devices, or entrapped air moves within the system. The longer the pipe line and the faster the fluid is moving, the greater the potential for shock.
Surges in pressure place stress on piping materials and joints and can cause the piping system to physically move. Engineering designs must incorporate controls that can maintain surge pressures within the piping system’s capabilities and eliminate or minimize the system’s physical motion.
Engineers have several options when designing piping systems to help minimize surge pressure. Properly sizing pipes is the most effective way to control fluid velocity. The larger the pipe diameter, the slower the fluid velocity for a given volumetric flow rate. This variable should be adjusted to maintain the required flow rate while keeping surge pressure below 1.5 times the piping material’s maximum working pressure.
Linear fluid flow velocity within the piping system should generally be limited to 5 ft/s for power generation plants, especially for pipes six inches or larger. Air should never be allowed to accumulate in the system while it is operating. During start up, the fluid velocity should be limited to 1 ft/s while filling or until all air has been flushed out and the pressure has reached operating conditions. Pumps should never be allowed to draw in air.
Extra protective equipment – pressure relief valves, shock absorbers, surge arrestors and air vacuum relief valves -- may be used to prevent surge pressure or fluid hammer in pipes. Fast acting valves should always be regulated to help prevent hydraulic shock.
Selecting Piping With a History of Performance
Quality matters when it comes to piping systems installed in power generation plants. Corzan CPVC has the engineering to resist a range of corrosive chemicals and the heat and pressure common to power plant environments. The piping system is backed by a 60-year history of reliable service within the power generation industry to boost user confidence and improve bottom-line performance.
Determine whether Corzan CPVC is right for your power generation plant application. Contact a Corzan Engineering Expert for a free process suitability review and technical assessment.
Details for this blog were taken, in part, from the following:
https://www.corzan.com/blog/understanding-surge-pressures-in-piping-systems
https://www.corzan.com/blog/what-is-corrosion
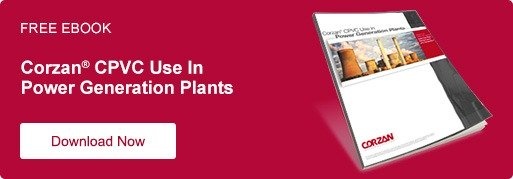