Corrosion Resistance
Corzan® CPVC Innately Resists Corrosion and ScalingUnlike metallic alternatives, Corzan® CPVC innately resists corrosion and scaling, protecting you from costly remediation, inefficiencies and danger.
What are Corrosion and Scaling?
Corrosion is the deterioration of material – primarily metal – resulting from various reactions that occur between the material and its surrounding environment. There are several types of corrosion:
- Internal Corrosion – Generally caused by the medium the piping system is transporting, any fluid with pH levels outside of neutral (+/-7) may cause metals to corrode, and ions within acidic (pH < 7) and alkali (pH > 7) fluids and saline solutions attack specific metal elements at the molecular level and eat away at the material. The attack accelerates in the presence of dissolved oxygen and higher temperatures. High-purity water systems can also cause corrosion in metallic pipes, as it will try to strip away metallic ions.
- Pitting Corrosion – This type of internal corrosion causes localized, small pits or cavities to form due to film damage. This is a highly penetrative, very dangerous form of corrosion that can cause extreme failures with little warning.
- Crevice Corrosion – This is a type of internal corrosion in which deterioration occurs at any crevices, as where two different materials meet. Stagnant liquid in the crevices accelerates this form of corrosion.
- Flow-Accelerated Corrosion (FAC) – FAC is caused by turbulent flows common with the typical higher pressures, temperatures and fluid velocities in industrial applications.
- Under-Deposit Corrosion (UDC) – UDC occurs when localized pitting and corrosion forms underneath existing solids, which then deposits in boiler tubes.
- Galvanic Corrosion – Also known as bimetallic corrosion, galvanic corrosion is an electrochemical reaction where one metal corrodes another due to electrolyte exchanges when the dissimilar materials meet. This is a common form of corrosion when different metals (a cathode and an anode) are joined.
- Microbiologically Influenced Corrosion (MIC) – MIC is caused by the metabolic activity of microorganisms that live in the biofilms on the inside surface of pipes. MIC can introduce harmful byproducts into a piping system that will induce some of the types of corrosion defined above.
- Ambient or External Corrosion – This is any form of corrosion caused by the external environment in which the system exists. For example, systems may corrode from the outside to the interior in environments that are close to large bodies of water and salt water, as with ships and offshore platforms. Ambient corrosion is also more likely to occur in cold environments where insulation is applied to the outside of metal piping to protect it from freezing. Improperly properly designed and installed insulation often allows moisture in but not out, resulting in corrosion under insulation (CUI) in insulated metal piping.
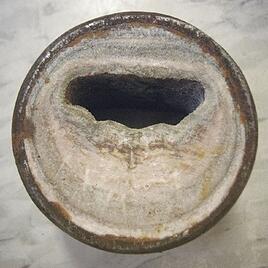
The Consequences of Corrosion
Corrosion is a widespread and expensive problem impacting every industry around the globe. The 2016 NACE International IMPACT study estimated the global cost of corrosion at approximately $2.5 trillion USD. Corrosion affects flow rates and efficiency while weakening pipes, which can result in costly downtime and expensive repairs. Metallic ions introduced to a product stream can produce off-spec products or products unable to perform as expected. In a latex paint facility, for example, metal may contaminate paint, resulting in biological growth or fouling of the product.
Corrosion can be dangerous to more than just finances. Corrosion may also cause loss of containment (LOC), leading to leakage or streaming of liquids (including acids). Many acids are clear like water, and an unsuspecting worker could be hurt badly by acid leaking from a pipe. Corroded bits of metal can also affect any reactions taking place in the system, such as acting as a catalyst for an immediate exothermic reaction resulting in a dangerous level of heat.
Corrosion and scaling present water contamination dangers as well. Corrosion can lead to dangerous lead and copper contamination when pipes made of these materials are part of the potable water ecosystem. And the microbial slimes and biofilm that can form in metal piping foster the growth of bacteria that can cause MIC or serious illness, like Legionella.
The Difference You Can See
The chemical makeup of Corzan CPVC lacks the conditions that cause corrosion. Its smooth surface finish also adds resistance to scale build-up. Corzan CPVC has a Hazen-William C Factor (which measures surface roughness) of 150 and can maintain this rating throughout its entire service life. New cast-iron piping, by contrast, is rated only at 120, and this number can drop to 60-80 after the piping becomes worn or pitted. The friction losses through the piping system increases as the C Factor decreases.
Adding Corzan CPVC as a tank lining or using it in dual-laminate piping mitigates many of the corrosion problems experienced with metals. In dual laminate piping, a thermoplastic liner serves as the pipe’s interface with a liquid or medium. When Corzan CPVC is specified, the material’s inherent resistance to many of the aggressive, highly corrosive fluids used in chemical processing systems makes it ideal for these demanding applications. The Corzan CPVC liner is then reinforced on the outside with a fiberglass reinforced polymer (FRP) shell. The fiberglass is applied with a bonding resin and, when cured, forms a solid exterior. This creates a pipe that is both relatively lightweight and structurally strong.
While Corzan CPVC has lower thermal conductivity than metal, code compliance may still require insulation. But even if there is a break in the insulation vapor barrier or if it is installed incorrectly, Corzan CPVC will not corrode under insulation.
As for scaling, the elements within Corzan CPVC material do not attract the metal ions or minerals, keeping the interior of the pipe free of buildup.
Two pipes after years in use for wastewater treatment. The metal pipe (left) is severely corroded, while the Corzan CPVC pipe (right) has maintained its surface smoothness and inside diameter.
To get a long, reliable service life, choose a material that naturally resists one of the most expensive problems of metallic alternatives: corrosion resistant Corzan CPVC.
Corzan CPVC Stands Up to the Harshest Chemicals
Corzan CPVC is tested against over 500 chemicals and compounds for suitability and formulated to effectively stand up to most acids, bases and salts. It is also innately resistant to corrosive chemicals, including the 10 commonly used chemicals that can degrade and reduce the service life of many metals.
Select a chemical to explore why Corzan CPVC is the more suitable choice.