How To Design an Industrial Piping System for Ideal Flow Rate and Velocity
In industrial plants, we often discuss what is being conveyed in the pipe as a function of system design. How a material performs with respect to corrosion and temperature resistance when interfacing with different fluids is a significant consideration during system design.
Nearly equal in importance is how the fluid is moving through the pipe. Flow rate plays a significant role in determining a system’s longevity, as well as its day-to-day energy consumption.
Understanding the efficiency with which a fluid can pass through a piping material is a significant step toward ensuring the long-term reliability and cost savings potential of certain materials.
Fluid Dynamics: Important Terms
When discussing the efficiency of fluid running through a pipe, it’s important to establish the definitions of a few terms up front:
Flow Velocity: Velocity is the most straightforward term, as it is the average speed of a fluid flowing through the pipe. Think of flow velocity like you consider the speed of your car. Except, instead of recording flow velocity in MPH or km/h, fluid is typically in m/s or ft/s.
Flow Rate: This is the volume of fluid that passes through the pipe per unit of time, recorded in m3/s or ft3/s.
As the equation below shows, flow rate is positively correlated with velocity—as the speed of the fluid increases, the amount (or volume) of fluid passing through the pipe during a given time period also increases.
Fluid Pressure (Fluid Head): Technically, pressure head is the amount of energy within the fluid caused by pressure put on it. This is most relevant when considering pressure loss, and the corresponding pressure drop.
- Pressure loss (head loss): This refers to how much the forces—including turns, valves and friction from the pipe wall—reduce pressure.
- Pressure drop: This is the difference in fluid pressure between two points in the system caused by pressure or head loss.
What Factors Influence Flow Rate?
One common factor in flow rate design is the size of the piping systems. To reduce capital costs, some engineers may decrease the pipe size to increase the flow rate. Adversely, higher flow rates can diminish the life of metallic system due to erosion and possible surge pressures.
In plastics, erosion is typically not a concern. Rather, there are design targets that need to be considered based on the type of plastic.
To optimize the flow rate, some engineers attempt to minimize how much pressure is lost throughout the system or the pressure drop from one point to another.
Friction (f): Friction against the fluid flow is wasted energy. The friction factor cannot be changed by system configurations or designs, and is a constant for each material in this equation.
Pipe length (L). Friction pushes against the flow, resulting in pressure loss as the pipe length increases. Pipe length also factors in fittings, which increase the “length” input for the equation.
Velocity of fluid (v): As flow velocity increases, pressure loss also increases and efficiency decreases. The general rule of thumb is to maintain a velocity below 5 ft/s (1.5 m/s).
Gravity (g) and the slope of the pipe. An increase in slope decreases the pressure due to gravity.
Pipe Diameter (D): The larger the pipe diameter is, the slower the flow velocity will be. Optimal flow rate can be maintained without increasing the velocity, if a larger pipe is specified.
Why Is Flow Pressure, Rate and Velocity Important for Industrial Applications?
In general, engineers try to design systems that balance cost with efficiency and reliability. In other words, which specific system will (a) fit a budget, but not (b) inflate energy consumption and also not (c) require excessive repairs and maintenance in the future.
Efficiency
Proper piping material selection and system design controls the flow rate and velocity in a way that minimizes energy costs. Reasons for this:
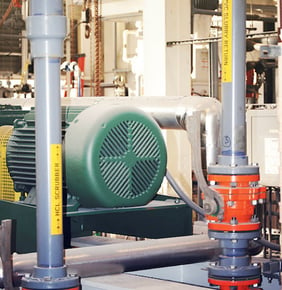
- Faster fluid translates to greater friction loss, increasing stress on pumps. More energy will be consumed and larger pumps may need to be installed.
- Certain materials, such as metals, will corrode more quickly at high speeds. Corroded materials are less smooth and thus create more friction loss.
Reliability and Service Life
Decreasing the velocity of fluid in an industrial piping system not only improves efficiency, but can also reduce the likelihood of pipe damage.
Fast moving fluid creates a potential liability to the dependability and service life of metallic piping system:
- Because higher fluid velocity can promote corrosion, piping may need to be repaired or replaced sooner than expected.
- Similarly, piping worn by abrasives and erosion may cause premature failure.
- At bends and turns, fast moving fluid can damage the system and lead to pitting and other problems.
- Hydraulic shock, or water hammer, occurs from a sudden change fluid velocity, and the related surge pressure is more devastating at higher speeds.
In general, higher fluid velocities result in worse efficiency—increasing energy expenses—and lessen system reliability—as damage to the pipe becomes more likely.
Upfront Cost
The main elements that determine piping costs are the material type, pipe size, material amount and the installation.
If money was no object, a system could be significantly over engineered with very large pipes. This would keep the fluid moving slowly and experience very little friction loss, but would be very expensive to purchase and install.
This is why the relationship between fluid flow, operating costs and upfront costs is a balancing act.
How CPVC Optimizes Industrial System Flow
To compare one piping material to another for optimizing flow rate, smoothness of the piping interior from installation through its service life is the most relevant factor.
The coefficient used to compare materials is the Hazen Williams C-Factor—the higher the coefficient, the smoother the pipe service. The following formula is used to calculate water velocities, head-losses and pressure drops, where “C” is the material’s Hazen Williams C-Factor.
CPVC has a C-Factor of 150 at installation, and that smoothness remains fairly constant throughout its life. Stainless steel, however, has a C-factor of 130 at installation, but that can dip considerably over its life.
Metal is more likely to lose smoothness and consistency over time due to its inherent proneness to scaling and corrosion.
See How CPVC Compares to Metal
Optimizing the flow rate of an industrial piping system is one important factor to an efficient system. In the resource article, Metal v. CPVC Piping Systems — Can CPVC outperform metal piping in industrial applications?, our team of engineering and product experts compare CPVC piping to metal in terms of temperature, pressure, and corrosion resistance, cost and safety.