Metal v. CPVC Piping Systems
Which Piping Material Performs Better In Industrial Applications?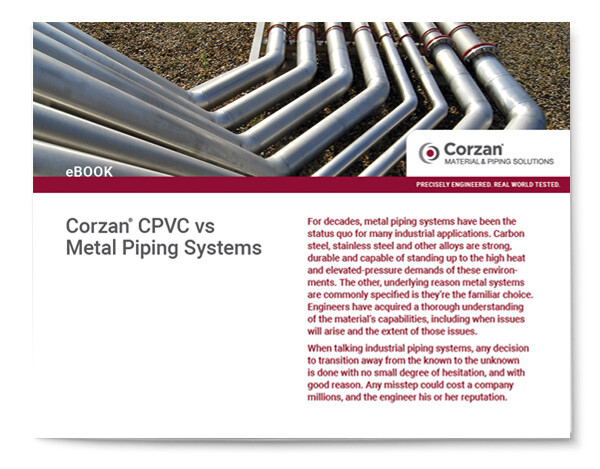
Introduction
For decades, metal piping systems have been the status quo for many industrial applications. Carbon steel, stainless steel and other alloys are strong, durable and capable of standing up to the high heat and elevated pressure demands of these environments.
The other, underlying reason metal systems are commonly specified is they’re the familiar choice. Engineers have acquired a thorough understanding of the material’s capabilities, including when issues will arise and the extent of those issues.
When talking industrial piping systems, any decision to transition away from the known to the unknown is done with no small degree of hesitation, and with good reason. Any misstep could cost a company millions, and the engineer his or her reputation.
The Opportunity Cost of Metal
That said, the opportunity cost of sticking with the tried and true may be equally as detrimental. Many industrial applications—including chemical processing, chlor-alkali processing, mineral processing and power generation—are realizing tremendous value from piping systems constructed of chlorinated polyvinyl chloride (CPVC).
More specifically, industrial plants are lowering installation costs, experiencing less downtime and improving process efficiency thanks to a transition to CPVC piping, fittings and valves.
How Can Plastic Outperform Metal?
CPVC technology was specifically engineered to satisfy the demands of harsh industrial process environments. In 1958, Lubrizol was the first to formulate CPVC into a useful material for pipes and fittings. Corzan® CPVC is a thermoplastic capable of withstanding prolonged exposure to high heat and elevated pressure while offering superior corrosion resistance.
This page was written to detail how CPVC is comparable to metal and where it distinguishes itself. It also looks to dispel some myths about the material’s misperceived weaknesses.
If you’re considering CPVC for your industrial system or even questioning whether to stick with metal, hopefully this page can provide guidance and answer a few questions.
Table of Contents
What is Chlorinated Polyvinyl Chloride?
Chlorinated polyvinyl chloride (CPVC) is an important engineering thermoplastic due to its relatively low cost, high glass transition temperature, high heat distortion temperature, chemical inertness, and outstanding mechanical, dielectric, and flame and smoke properties.
Conceptually, CPVC is a PVC homopolymer that has been subjected to a chlorination reaction. Typically, chlorine and PVC react according to a basic free radical mechanism, which can be brought about by various approaches using thermal and/or UV energy.
The chlorine content of base PVC can be increased from 56.7 percent to as high as 74 percent, though typically most commercial CPVC resins contain 63 to 69 percent chlorine. As the chlorine content in CPVC is increased, the glass transition temperature (Tg)—temperature region where the polymer transitions from hard, glassy material to a soft, rubbery material—increases significantly.
The additional chlorine atoms protect the polymer’s carbon backbone against chemical attack, and give it greater heat resistance. The increased heat resistance allows CPVC to be pressure-rated at higher temperatures. The compound is also inherently inert to acids, bases, salts, and aliphatic hydrocarbons, all of which tend to corrode metals.
Diagram of CPVC (left) at a molecular level compared to PVC (right). The red spheres represent chlorine elements.
CPVC resin is then combined with additives. The quantity and combination of these additives modify many of the CPVC resin’s inherent properties, while easing its processability.
Temperature and Pressure Resistance
A material’s ability to withstand high heat and pressure for prolonged periods of time is essential to the performance of an industrial system. Any weakness here and plant operation managers will be regularly performing repairs, shutting down the system for unscheduled maintenance, and potentially replacing the piping system prematurely.
Metal has proven itself capable of satisfying heat and pressure requirements, but what about CPVC?
Setting the Standard
Every piping material must empirically validate what level of internal pressure it can withstand. For thermoplastics, both ASTM and ISO publish methods for pressure rating thermoplastic piping materials, but ASTM D2837 (“Standard Test Method for Obtaining Hydrostatic Design Basis for Thermoplastic Pipe Materials or Pressure Design Basis for Thermoplastic Pipe Products”) is most commonly used in the United States.
According to ASTM D2837, a piping material’s pressure-bearing capability is determined by subjecting a number of samples to a range of pressures which will cause the pipe to rupture at times ranging from a few hours to over 10,000 hours. The data is analyzed using linear regression analysis, and the stress required for a lifetime of 100,000 hours (the Long Term Hydrostatic Strength or LTHS) is determined by extrapolation. Using the LTHS, a hydrostatic design basis (HDB) category is defined for the material using the following ASTM table.
A design factor (often referred to as a “safety factor”) of 0.5 is then multiplied to the material’s HDB psi to determine the maximum allowable stress on a material, or the Hydrostatic Design Stress (HDS), for water applications.
This design factor is based on two groups of conditions:
- Manufacturing and testing variables, specifically normal variations in material, manufacture, dimensions, good handling techniques, and evaluation processes.
- Application and use variables, specifically: installation, environment, temperature, hazard involved, life expectancy desired, and degree of reliability selected.
According to ASTM, this design factor defines what the material is “capable of withstanding continuously with a high degree of certainty that failure of the pipe will not occur.”
CPVC is pressure rated in this way with water at both room temperature (73°F) and 180°F. A derating table is provided for other temperatures within the material’s operating range.
Following is Corzan CPVC’s maximum operating temperature and pressure range as determined by ASTM D2837. The red area is what most engineers perceive CPVC’s capabilities to be. The light gray is Corzan CPVC’s actual full operating range.
CPVC Advantages Over Metal
Corrosion
The most significant advantage a CPVC piping system has over metal alternatives is its corrosion resistance.
Metal piping systems stand up fine to clean water processing applications with a neutral pH. However, as soon as a fluid’s pH extends much outside of neutral (~7) or salt is introduced (e.g. brackish or sea water), metals start to corrode and can degrade relatively quickly.
Reason being, ions within acidic (pH < 7) and alkali (pH > 7) fluids as well as saline solutions are able to react with many metals, causing corrosion. This attack is accelerated when dissolved oxygen is present.
Conversely, pipes and fitting made with CPVC material are inherently inert to most acids, bases, and salts, meaning the aggressive ions that attack metals flow right past CPVC, leaving the piping unscathed.
Metal Corrosion:
Metals may corrode by pitting corrosion wherein tiny pits form along the length of the pipe diminishing the pipe’s wall thickness and reducing its pressure bearing capability.
Another cause for concern is crevice corrosion. This is where ions in the fluid concentrate in crevices around welds, flanges and other types of pipe connections. This ion buildup can degrade material quickly causing leaks at welds and joints.
Consequences of Corrosion
The effects and severity of corrosion within a piping system will vary depending on the application, but generally speaking corrosion can lead to the following issues:
- Pressure rating decreases on account of thinning pipe walls.
- Flow rate can be slowed demanding more from pumps.
- Fluid purity can be contaminated as the corroded pieces float away. This is a significant concern for applications with high purity standards.
- Installation costs will increase, as highly skilled laborers are required to weld the system. This level of craftsmanship comes at a significant cost, a cost that is increasing as the most experienced welders near retirement.
Other considerations:
- External Corrosion: A big issue for plants in coastal regions, salt content in the atmosphere can eat away at a metal pipe’s exterior. In some areas, plants resort to painting external piping annually to protect its surface.
- Oxidative Layer Protection: Some metals naturally develop an oxidative layer over their surface, or additives can be applied manually to create this layer. This oxidation helps to fortify the pipe by creating armor around it that’s impervious to attack. This armor can help protect a pipe against pH levels slightly outside of neutral, extending its operating range. However, even oxidation layers can’t stand up to more aggressive acids and bases.
Scaling
Scaling is another significant threat to industrial piping, as it can significantly jeopardize flow rates.
At different pH levels and temperature ranges, certain metal ions are water soluble, which allows them to flow through a metal piping system with little to no problem.
However, if the fluid a metal is dissolved in falls outside of its solubility range, ions can drop out of the solution and attach to the walls of a metal pipe. These ions build up over time to create what look like scales around the inside of the pipe.
Processes that involve magnesium, calcium, iron, aluminum and silica tend to be at higher risk of scaling. Calcium, for example, has a very narrow range of solubility, creating a huge propensity to drop out of a solution.
Scaling tends to occur where there is eddying in the flow. These eddies can be found near imperfections in the pipe, such as around seams and flanges. As the fluid swirls around these eddies, a concentration of ions develops, increasing the likelihood of scaling.
With CPVC, there is little concern of scaling. The material has a significantly lower affinity to scaling than metals.
Did you know?
Pipe and fittings have a Hazen-William C Factor Rating, which is a measure of flow friction—the higher the rating the lower the friction. Corzan piping's rating is 150, and it can maintain this rating throughout its life. Conversely, new cast iron piping only has a rating of 120, which can drop to 60-80 if it's worn or pitted.
Consequences of Scaling
As scaling builds up, the pipe diameter can be constricted and your system will experience several detrimental side effects:
- Pumping efficiency decreases.
- Pressure will increase within the system.
- Scales can flake off and clog up filters or contaminate the fluid itself.
- As with corrosion, highly skilled laborers will be needed to create smooth seam welds to avoid scaling issues, which increases overall installation costs.
Installed Cost
Labor, fabrication and other installation expenses can combine to account for more than half of a piping system’s total installed cost. The following graph with data produced by Chemical Engineering Magazine shows the cost index of installing Corzan 6-in. CPVC piping systems compared to metal and thermoplastic alternatives.
When it comes to installation, CPVC holds a number of advantages over metal alternatives. Following is a look as to why a Corzan system offers one of the lowest installed costs of any piping material.
Joint Welding
Metal piping seams are welded together using intense heat and often a metal filler. This process carries with it two issues:
- To help limit the chance of corrosion or scaling, specialized welding techniques and equipment are required. The highly skilled laborers needed to make these welds are in high demand and costly.
- Often, hot work permits must be obtained in rated areas, which can be a hassle and expensive to acquire.
On the other hand, a CPVC system is fused together using a straightforward, two-step solvent cement process. The solvent cement is not glue. Instead it creates a chemical bond that fuses the two pieces together. Once cured, the joint actually becomes the strongest part of the piping system because the wall thickness is twice that of a single piece of pipe.
While solvent cementing requires some training, the training can be done onsite in less than 15 minutes, and requires no specialized equipment.
Should welding be required to join the CPVC piping, hot air welders are used, eliminating the need for a flame.
Weight
CPVC weighs 1/6th that of comparably sized steel. A 6-in., schedule 80 Corzan pipe weighs about 6 lbs./ft., whereas the equivalent steel pipe can weigh between 25 and 29 lbs./ft. (based on a sampling of steel piping manufacturers).
In other words, the weight difference between a 50-ft. piece of Corzan pipe and steel pipe is approximately 1,150 lbs. This translates into fewer workers needed, limited heavy machinery (if any), and increased laborer safety.
Required Labor and Equipment
The weight of a metal piping system requires that more laborers be involved to handle, install and secure the piping. In addition, heavy machinery will need to be available to transport and hoist the piping into place.
In addition, labor costs escalate as laborer skill-level demands increase. This is especially relevant for seam welds.
Fabrication
Due to its weight, need for specialized welding techniques, and electricity / flame requirements, much of a metal piping system is prefabricated offsite and trucked to the facility.
This process can prove expensive as special accommodations are made to ship the piping. In addition, there is limited room for error. Any miscalculations or assembly mistakes made offsite may lead to costly fixes onsite.
CPVC can be prefabricated, but thanks to its two-step solvent cement welding process and the fact that the material can be easily cut, onsite fabrication does not complicate the installation process.
In fact, CPVC material offers installers flexibility to course correct as necessary without any expensive reconfigurations.
Maintenance
Over the course of a piping system’s life, regular maintenance is required whether you choose a metal piping system or CPVC. Common maintenance may include integrating a new piece of equipment, layout alterations, or replacing sections that are accidentally damaged.
However, a CPVC system offers greater value than metal piping when it comes to maintenance work. With metal piping, you often must contract with a pipe fitter, and they may be required to reconfigure some connections or welds. In addition, the metal system is inflexible, so subtle alignment adjustments may require expensive reconfigurations.
With minor training for solvent welding of CPVC pipes and fittings, any mechanical contractor or plant maintenance engineer can change, repair and modify the system. The piping itself is also flexible to a point, so one or two men without specialized equipment can easily make alignment adjustments.
Safety
CPVC also offers a number of safety advantages over metal alternatives.
Thermal Conductivity
CPVC has a very low thermal conductivity value. The heat transfer coefficient of Corzan CPVC is approximately 1/300th that of steel, saving energy costs and offering a much cooler surface temperature. Not only does this also reduce the need for costly insulation, it limits worker exposure to burn hazards.
Fire Safety
CPVC will not sustain burning. This is thanks to its Limiting Oxygen Index (LOI) of 60. LOI is the percentage of oxygen needed in an atmosphere to support combustion.
Since Earth’s atmosphere is only 21 percent oxygen, Corzan pipe or fitting will not burn unless a flame is constantly applied to it, and it will stop burning as soon as the ignition source is removed.
Lightweight
CPVC is lighter to maneuver. This helps to reduce worker strain and injury during installation. It also eliminates the need for heavy equipment during installation.
No Flame or Ignition Source
CPVC systems require no open flame or ignition source to install. Instead, the system is quickly, easily, and safely joined via solvent cement, threading or flanging.
It is recommended that solvent cement be used in a well-ventilated area.
Debunking CPVC Piping Myths
Part of the reason metal piping systems are so prevalent is that there are some misconceptions about CPVC, and thermoplastics in general. We’d like to debunk some of these myths.
CPVC can’t stand up to high temperature and pressure
Corzan CPVC pipe and fittings offer the strength to meet the pressure requirements of process applications, even at elevated temperatures. It has proven itself reliable in hundreds of real world applications as well as by satisfying ASTM standards.
CPVC can’t stand up to prolonged exposure to sunlight, wind, rain and humidity
While not all CPVC compounds contain additives to overcome weathering, Corzan material is blended with a significant concentration of both carbon black and titanium dioxide, which are recognized as excellent UV blocking agents. These additives help to protect the polymer’s carbon backbone from the effects of UV radiation.
CPVC can’t be used for all piping system parts
CPVC is manufactured using straightforward injection and compression molding techniques. Many manufacturers have the capability to create any pipe, fittings or valves necessary for an industrial system.
For industrial applications, this means that an entire system can be constructed of Corzan material. A single material for all components limits complication and avoids costly configuration workarounds.
CPVC is too expensive
While CPVC may have a higher material cost than some metals, material is only part of the overall lifecycle cost of a piping system. Installation, maintenance and life duration also need to be factored in.
When all piping system costs are factored in, a Corzan system can generate significant saving over metal alternatives, as well as other thermoplastics.
Not All CPVC is Equal
It is important to note that not all CPVC performs the same. CPVC compounds are made with base resins that have different molecular weights and varying chlorine contents, as well as different compound additives that can affect their compatibility and long-term performance.
To ensure the system’s long-term performance, it’s recommended that you check with your piping supplier to determine what specific tests the pipe manufacturer has performed on its finished product. These tests include:
- Minimum burst pressure requirements
- Dimensional tolerances
- Residual stress requirements
- Drop impact requirements
- Fusion property testing
Delivering Reliability
Lubrizol is the pioneer in CPVC technology. We engineered the compound nearly 60 years ago, and have spent decades continuously honing and evolving its capabilities.
Today, Corzan CPVC is relied on for industrial applications spanning many industries, including: chemical processing, chlor alkali processing, mineral processing, power generation, semiconductor and wastewater treatment.
In addition, when choosing a material, it’s important to look for support beyond the product. Corzan Material and Piping Solutions’ team of regional product and engineering specialists are always available to provide expert advice, information and training throughout the life of a piping system.
If you’re interested in learning more about Corzan CPVC, or simply have questions about the process of transitioning away from a metal piping system, we’re happy to schedule a time to talk.